Supply Chains Are in Crisis, but Logistics Bosses Are Doing Better Than Ever
Pre-Christmas shortages have exposed the fallibility of global supply chains’ promise to deliver all manner of goods almost instantly. Yet logistics firms’ profits are at historic highs — showing how they’ve used the crisis to entrench their power.
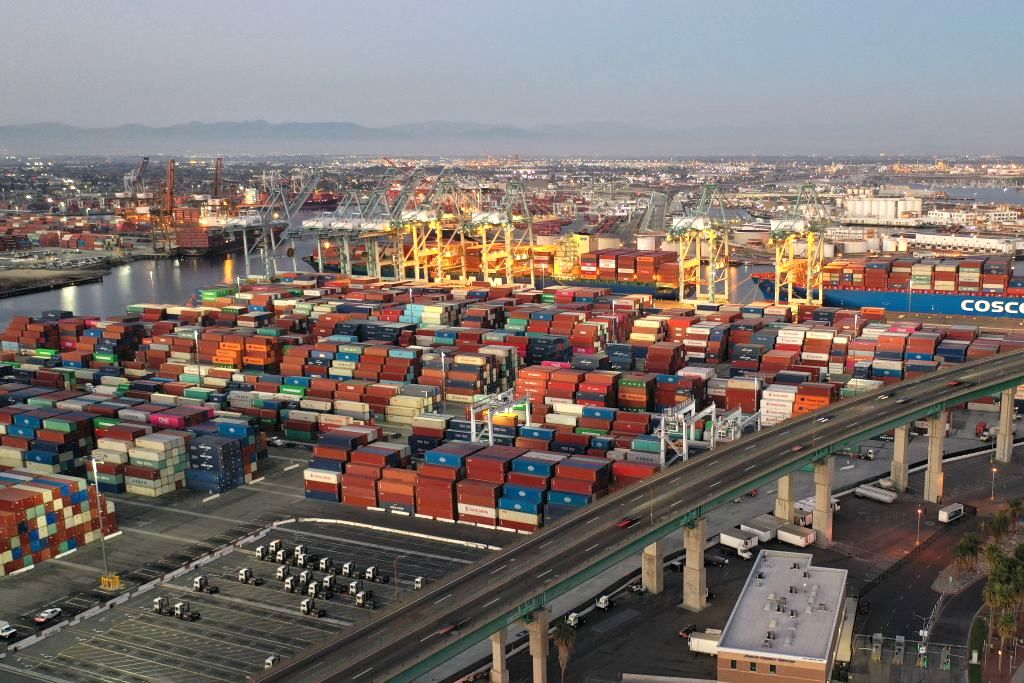
An aerial picture of the Port of Los Angeles in California. (Robyn Beck / AFP via Getty Images)
The supply chain crisis has affected the availability of everything from groceries to medical supplies and cars. Yet there’s also a casualty that’s harder to quantify — our children’s imaginations. Parents everywhere are breaking the news to their kids not only that Santa doesn’t exist, but that the ungreased wheels of global capitalism mean their Christmas is likely canceled this year.
But if America’s kids might feel like they’ve been hardest hit by this development, it also provides a bitter lesson for the Left. For despite all the cries about the crisis facing supply chains — and the litany of social media shit posts about supply chain issues being the root of all life’s problems — this holiday season, logistics firms are still raking in record profits.
The current crisis — most acute in the United States but affecting the whole world — is an inevitable reality of a global system built around delivering goods anywhere on the planet, nearly instantly. Indeed, this is how a global supply chain network built around flexibility is designed to work: its very agility and pervasive coverage makes it inherently vulnerable to crisis. This is just the first truly major global production crisis it’s faced. Explosive demand, lingering pandemic shortages, and tight labor markets in key sectors (not to mention many workers weighing whether it’s worth turning up) are putting previously unseen strain on the system.
For years, leftist geographers and labor organizers have argued that choke points on supply chains present vulnerable targets which, if exploited appropriately, could disrupt the entire flow of global capitalism. The fallibility of this system of production and distribution, initially largely confined to theory, has now been borne out in the real world on a mass scale. But just because we know the system’s weak points can be damaged doesn’t mean that organized labor, either in the United States or globally, is anywhere close to being prepared to exploit these weaknesses.
Cracks in the Supply Chain
A combination of issues has produced the most striking images of the crisis, from unloaded containers stacked perilously high at some of the world’s largest ports, to hulking container ships floating idly as they wait to bring their cargo to shore. At the height of this global gridlock a record 111 containers were waiting off Los Angeles and neighboring Long Beach ports, smashing the pre-pandemic high of seventeen. Roughly 40 percent of US container traffic comes through these southern California ports.
Though most acute in California, there have also been massive delays in ports from Savannah, Georgia to Newark, New Jersey — and, indeed, in Britain, the Netherlands, and China, with roughly six hundred cargo ships globally left waiting to unload at one point last month. Clogged ports created bottlenecks so dire that Joe Biden was roused from his nap to decree the LA and Long Beach ports would shift to 24/7 operations to ease pressure. And while a global, static flotilla loaded with late deliveries is hard to ignore, it’s only one factor in the crisis.
While in Europe consumer demand is yet to fully recover from the pandemic, it has exploded in the United States. This is partly due to the pandemic spurring rare, if inadequate, direct public support for consumers. US household income rose 10.5 percent in April 2020 amid mass joblessness and shutdowns, as beefed-up unemployment benefits kicked in, bringing many Americans more cash than they normally got at work. Similarly, consumer spending rose 4.2 percent on the back of the third round of stimulus investment this spring.
Most Americans spent more in 2021 than last year, while consumption of many goods has eclipsed 2019’s pre-pandemic levels. Global production has struggled to meet this skyrocketing demand, with various hiccups further slowing trade and heaping pressure on links in the supply chain. Thanks to high demand and the abundance of backed up ports, there’s even a shortage of shipping containers.
Given how much the pandemic has impacted nearly every facet of life all over the world, it’s a wonder that the Global North has only just begun to feel the supply chain crunch in earnest. The effects of the pandemic have, doubtless, been strongly differentiated across the planet. But just as COVID-19 initially spread along globalized routes of production and trade, the virus continues to impact global production. As the Delta variant spread to Asia this Spring, some of the busiest ports in the world were shuttered due to COVID outbreaks. Similar slowdowns have recently hit factories in China and Vietnam, key global industrial producers.
Knock-on effects of pandemic outbreaks straining extraction and production, along with sustained demand, have fostered further bottlenecks in supply chains. Prices for energy, so crucial to production and shipping costs, have soared, as have vital commodities like copper and steel. And though many of these commodity prices are likely to cool as their bubbles pop or supply catches up to demand, supply chains continue to face pressure from all angles. Meanwhile, attempts by logistics firms to skirt shortages via strategic hoarding have only exacerbated bottlenecks by generating scarcity at other points on the supply chain.
The Great Resignation
Possibly the key bottleneck is the one that has the most potential from the Left’s standpoint: labor. The United States is today in the midst of a so-called “Great Resignation,” with workers fed up with grim working conditions often gravely exacerbated by the pandemic. As a flurry of recent strikes suggest, this has frequently translated into organized labor activity. There have been more work stoppages in 2021 involving over a thousand workers than 2020, though it still trails significantly behind 2019 levels.
With so few US workers unionized, in many cases strikes do not seem to be a feasible course of action. Far more Americans have simply resigned, emboldened by a tightened labor market. In August alone, 4.3 million people, or 2.9 percent of the workforce, quit their jobs. Low-wage workers, many of them on the front lines during the pandemic, are at the forefront of this mass exodus.
Europe’s recovery has also spurred a tight labor market, albeit not on the same scale as the United States. Many central European countries have achieved near full-employment, putting pressure on Western European countries typically reliant on comparably cheaper labor from the ex–Eastern Bloc. While much of the Global North is struggling to find workers, vaccine apartheid means workers in the Global South are significantly more vulnerable to COVID-19, putting pressure on workers in key extraction and production segments of the supply chain.
This labor shortage has also wracked the logistics sector, with shortages of dockworkers and, especially, truckers. The United States is short more than sixty thousand truckers, vital for moving freight from ports to factories for finishing or across the country to warehouses for local distribution. This closing step in the supply chain isn’t just struggling in the United States. Europe is in need of four hundred thousand truckers, with Germany alone short eighty thousand.
As with many positions during the Great Resignation, there are actually enough certified truck drivers in the United States. It’s just such a brutal job that few people want to do it. Logging crushing hours for low pay, port truckers are typically classified as independent contractors, with few benefits and protections, forced to purchase their own equipment and compete with one another as atomized small businesses. This work looks particularly unattractive amidst the pandemic, especially as workers have a bit of leverage and can change fields. Trucking wasn’t always like this: drivers were typically standard employees until regulatory shifts in the 1980s made reclassification possible.
That working conditions for truckers have eroded even as their labor became a more vital part of the global economy is no coincidence: it’s part of a global race to the bottom caused by the so-called “logistics revolution.” The elements that make the entire system so vulnerable were seen as positives, until a crisis of this magnitude entered the picture.
Just-Too-Late?
Labor deregulations beginning in the 1970s and evolutions in transportation technology paved the way for today’s supply chain capitalism. The logistics revolution converged production and distribution into a single, comprehensive system of design, production, warehousing, sale, and circulation of goods to maximize profits.
Managing a cohesive system of production enabled companies to respond immediately to market fluctuations and squeeze profitability out of every step of the supply chain. Usually sold as boosting efficiency, this almost always came at the expense of workers’ wages, conditions, and power, regardless of their role in the process. This boosted profits tremendously; but the system is proving less durable in the face of today’s extreme market fluctuations.
The goal was to link supply and demand and eliminate friction between the two, conceptualizing the supply chain as a single system meant to continuously flow at all times. This is contingent on flexible, “just-in-time” production, where goods are produced on-demand, often with inputs at varying points on the now globalized process, to prevent overproduction. Why pay for goods to sit in depots when container ships can serve as floating warehouses and goods can immediately be moved on after arrival, ensuring the coveted one-day shipping?
Less friction might mean everything runs faster — but the flexibility that was once seen as the logistics sector’s greatest asset is now coming back to haunt it. Given that storing surpluses of goods is seen as antithetical to modern production and that maintaining an increasingly elaborate, world-spanning system drives capitalism, it shouldn’t be a surprise that a global pandemic ravaging supply, concurrent with tectonic shifts in demand, might cast this nimble system into crisis. Supply chains are doing exactly what they’re supposed to: agile flexibility is king, and agile flexibility is by default not robust.
The global nature of supply chains — pitting workers globally against each other, under constant threat of capital flight — has typically allowed manufacturers to circumvent crises. Constant circulation and interchangeable production meant a hiccup at one point of the supply chain could simply be avoided. Finish the product in Mexico, not Taiwan, import it in Oakland, not Long Beach, etc.
Logistics firms have further committed to flexibilizing their supply chains in the wake of the pandemic, with many developing “China plus one” strategies to ensure they’re not overly dependent on Chinese production. Now, though, every link is on fire, and backups or breakouts in China or the United States help slow down the whole system. This is a direct result of a system that can get a TV shipped to your door in less than twenty-four hours from nearly anywhere in the world.
Hammering the Weak Links?
The supply chain crisis hasn’t just frustrated holiday shoppers, or presented more serious challenges, like pushing heating costs for families or producing shortages in medical supplies. It’s helped prove the theory, long pushed by Marxist geographers, that supply chains are capitalism’s weak links.
For over a decade, names such as Kim Moody and Jake Alimahomed-Wilson have argued that the transition to a global, flexible supply chain under the logistics revolution has created vulnerable choke points capable of pressuring, or even stopping, global capitalism. Full disclosure: I, too, have made this argument. The current crisis has borne out the notion that these chokepoints are vulnerable targets.
Unfortunately, instead of this bringing hope to theorists and organizers in the logistics space, this crisis should give us pause. Yes, a spanner has been thrown in the works of global capitalism. But considering that a horrendous pandemic, still raging largely unchecked in most of the world, originated in the planet’s industrial center — intermittently grounding life to a halt for much of the world’s population — this crisis hasn’t exactly brought key players in the logistics sector to their knees, as shippers and retailers amass record profits. And though it’s hard to know for sure, there are signs indicating the crisis is already easing.
While we finally have evidence of the widespread vulnerability of supply chains, seeing just what it takes to seriously hurt them is an unsavory taste of reality for workers. Simply put, organized labor is nowhere near capable of putting a dent in the supply chain. Though most of those on the Left that call for exploiting the weak points in global capitalism generated by the logistics revolution are earnest about what a challenge this would be, the pandemic has demonstrated that a staggering crisis is required to make an impact. Labor has struggled to take advantage of this moment, and seems incapable of replicating a similarly serious challenge to the supply chain anytime soon.
While the hallmark of the supply chain crisis, overloaded container ships floating idly, waiting to deliver their wares, has materialized most remarkably in the United States, American labor is uniquely under-equipped to lead a global workers movement. With a union density of roughly 10 percent (and an even worse 6.3 percent in the private sector), organized labor in the United States is especially weak, even in the context of recent militant, headline-grabbing strikes.
Though organized labor’s implosion in the United States might have been more drastic than most other countries, it represents a broader trend. The average union density in OECD countries is just 15.8 percent, down from 20.9 percent in 2000. Though longshoremen jobs in western ports are often unionized, it’s usually a very different story for other positions along the supply chain, from resource extraction to assembly and delivery via ship, train, and truck.
The shifts brought on by the logistic revolution’s deregulation and emphasis on flexible production have almost always further atomized workers, ensuring that even as more sectors of the economy are sucked into supply chains, actually organizing these workers has gotten tougher. While the crisis should be a golden opportunity for labor, the changes that have created glaring weak spots in the global economy have also made it harder for increasingly nonunionized, subcontracted, and disconnected workers to leverage their dwindling power.
It’s not just a question of union density (or worker militancy, which doesn’t directly translate into union membership). Successfully challenging global capitalism means successfully coordinating workers’ movements internationally, adding another layer to the task. Usually, an overloaded port or occupied factory is simply bypassed for the next-closest option. It’s only now that nearly every port is overloaded and production has been halted at factories in entire regions, that we’ve seen tremors sent through the entire system.
Centralization in the sector means a few key firms have massive targets on their backs. Yet, their size and resources have helped them eviscerate unionization attempts. This is especially true of two US-based retailers that have helped drive the logistics revolution: Walmart and Amazon. The shift to just-in-time production reshaped the power balance away from manufacturers toward retailers, as goods are now produced so quickly that retailers can dictate exactly how much of and when a product is manufactured.
Walmart’s early adoption of just-in-time production allowed it to undercut competition and squeeze workers along the supply chain. The United States’ largest employer, it is now so influential on production it can fine suppliers for late — or even early! — deliveries. Amazon took Walmart’s model and adapted it to the digital age, and has only become more vital to the United States and world economy in the wake of the pandemic. Both have evolved from retailers to pivotal logistics firms in the global economy.
None of Walmart’s 1.6 million US employees are unionized (despite nearly two decades in labor’s crosshairs) and Amazon has proven equally adept at union-busting. While these retailers have outsized influence, labor has most frequently challenged them either at the point of sale or at distribution centers, toward the end of the supply chain where targets are most diffuse and easiest to circumvent.
Hurting them further up the supply chain would mean not just challenging two of the biggest, most ruthless companies on earth, it would mean organizing workers typically classified as independent contractors or employed by subcontracting firms. Despite their concentration on paper, they’re more thinly spread where it matters for labor — in their workplaces.
Lessons Learned
If mainstream news has suddenly become interested in logistics and labor struggles, it’s offered little insight as to what could solve the woes that supply chain capitalism inflicts on the world. The commentariat’s imagination seems limited to tepid pleas for Americans to consume slightly less.
A broader, critical understanding of the supply chains that have ensnared the planet must also be contextualized within this moment of growing workers’ consciousness. Amidst the Great Resignation, both worker militancy and media coverage of it have risen. Meanwhile, organized labor is in such shambles that it’s barely capable of taking advantage of a global crisis in production.
In the United States especially, individual workers have benefitted from a tight labor market and renewed militancy to find new jobs with better conditions and pay. Translating this into effectively organizing workers together has proven difficult. While pitched labor battles have spread to a much wider array of sectors than usually seen in the United States, the autumn “strike wave” pales in comparison to America’s industrial past.
Centering this militancy and identification on the importance of logistics work can only help inform a workers’ movement which has nowhere to go but up. There are also some good signs that further worker militancy, like election results in the Teamsters and UAW, could be on the horizon. This fight also desperately needs to build solidarity across national borders.
Some recent examples centered around ports demonstrate that labor internationalism is possible. But again, this consciousness — as well as organization and militancy among workers, in the United States and globally — is still far from able to truly challenge supply chain capitalism. This doesn’t mean that choke points in logistics shouldn’t be taken seriously, as the labor movement (hopefully) grows. But strategizing around challenging this seven-million-headed hydra needs to take seriously the limitations faced now and in the foreseeable future.
Labor can and must learn from this moment, but it is nowhere near ready to spark a challenge on the scale necessary to slow down, let alone stop, these structures. Hopefully the next crisis isn’t yet another learning opportunity, but a moment to act.