‘Tis the Season to Organize Amazon
During peak season, when Amazon’s holiday rush hits maximum velocity, the company’s finely tuned machine becomes surprisingly fragile. For workers seeking to organize, the high-stakes holiday months may be their strongest opportunity to exert leverage.
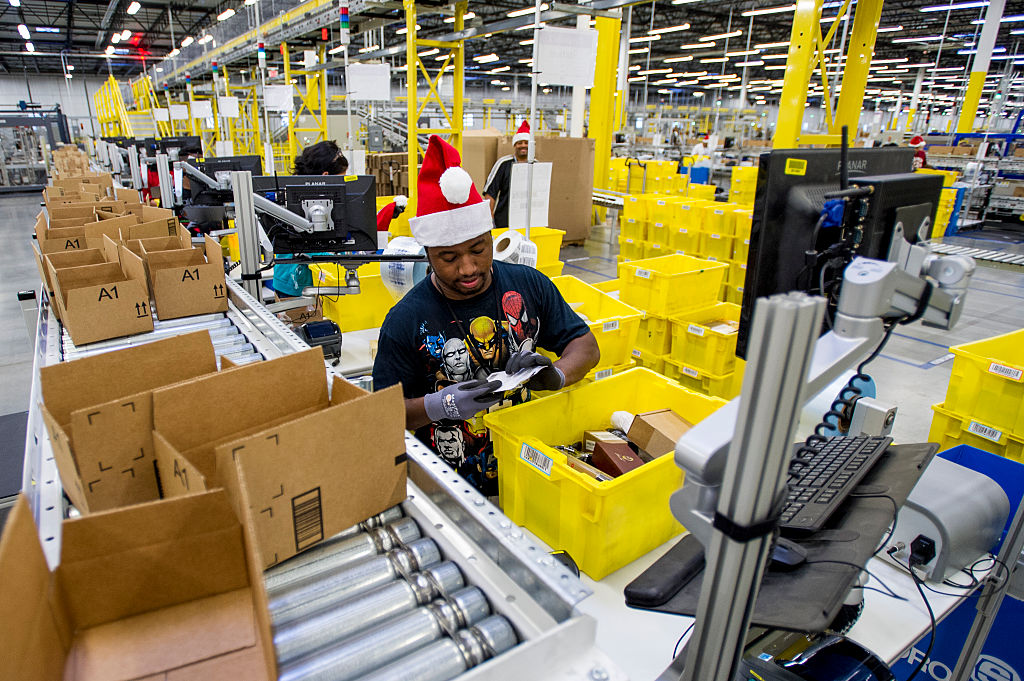
An employee loading boxes at an Amazon fulfillment center during the holiday season in Tracy, California. (David Paul Morris/Bloomberg via Getty Images
I recently toured an Amazon fulfillment center; anyone can do it. From what I can tell, they mostly give tours of their robotics sortable facilities, the newer ones dominated by Kiva robots and other automation technologies, to give the sense of a company doing what was barely imaginable a decade ago.
And to Amazon’s credit, it is a truly impressive affair. In the three-million-square-foot fulfillment center I toured, conveyor belts ran the length of the facility. From one end of the building, you could barely make out packages moving along them as any more than little specks. On many levels, stowing and picking stations surround a fenced-in center area dominated by Kivas, all carrying 2,000-pound stacks of goods, ready at the click of a button to move to the closest picking station to fulfill an order. For the moment, the robots are mostly separated from the people for safety reasons, but the new autonomous Proteus robots will soon change that.
I heard many impressive facts on the tour, but there was one that really stuck with me: this facility had been open for a year, and it was running at about 30 percent capacity. If the facility were pumping out 300,000 packages per day outbound (I didn’t catch the exact number, but it’s a reasonable estimate for a sortables facility of this size), it could handle a million. This apparently is not an uncommon situation: Amazon reserves extra capacity at its fulfillment centers for peak season, roughly from late October through Christmas, when it can sometimes see more than twice the normal volume demand.
From a labor organizing perspective, this is a terrifying situation. It means that, for most of the year, if you did the hard work of organizing a strike by the thousands of workers at any given Amazon fulfillment center, it would hardly register on Amazon’s radar — not because the company has the resolve not to flinch in a labor dispute, but because they could so efficiently reroute order fulfillment to other facilities that it would likely not slow down their operation in any noticeable way.
Fulfillment Centers, especially the highly automated sortable ones, are huge capital investments, but they are also highly immune to disruption. Amazon recently executed a regionalization strategy to cut down on long-range order fulfillment, but before that, roughly 40 percent of orders at a fulfillment center were going out of region. If need be, Amazon would not hesitate to let the long-range fulfillment percentage creep back up again.
This kind of situation contrasts markedly with that of the ports, where shippers and carriers can and move volume around when they anticipate disruption — as they did, for instance, during the recent East and Gulf Coast port strike — but where their ability to do so is extremely limited by existing capacity. Compared to the massive Chinese ports, American ports currently don’t have a great ability to cope with great volume shifts. This is to the decided advantage of the longshore workers’ unions, but it only further highlights the precarious position of Amazon fulfillment center workers.
Now this might make the prospect of organizing Amazon warehouses appear somewhat bleak, were it not for two additional considerations: First, Amazon operates many other kinds of facilities, ones that are either far fewer in number than the fulfillment centers or much more place-based than them. Not everything is fungible in Amazon’s distribution network, as I explain here, and we do ourselves a disservice to think about Amazon logistics solely in terms of fulfillment centers (indeed, given the tours it offers, as Amazon itself appears to want us to think about it).
And second, there is one opportune time every year to make Amazon really feel the pressure, and that is the holiday season that’s just around the corner. Transport geographer Jean-Paul Rodrigue illustrates the dramatic package volume increase between Thanksgiving and Christmas in the chart below.Amazon is in the process of trying to hire a quarter of a million people in preparation for the holiday season, at which point its logistical operation will be in full swing. Peak season is a uniquely vulnerable time at Amazon: they need workers, and they’re as close to operational capacity as they’re going to get. The holiday season is, of course, a busy time for all retailers, but this fact is particularly pertinent in the case of Amazon because it is the one time during the year when certain components of its distribution system are vulnerable to disruption.
To organize a corporate behemoth like Amazon, the labor movement must understand the interrelation of the different elements comprising Amazon’s network, each of which presents its own vulnerabilities, but it must also take advantage of timing. Thus far, to my knowledge, only episodic coalitional campaigns like Make Amazon Pay have attempted to do so on a broad scale, relying on independent groups of workers to participate in international days of solidarity. Such campaigns are good awareness-raising mechanisms, but they are flashes in the pan without deep organizing and institutional roots.
In the United States, any serious campaign to organize Amazon is going to require the central coordination of the International Brotherhood of Teamsters, which has public organizing efforts at multiple delivery stations and Amazon’s central air hub, KCVG. These efforts must be massively scaled up to meet the challenge of Amazon, and they must also exploit the key stretch of the calendar year that is upon us.