In UAW’s Negotiations With the Big Three Automakers, Ending Tiers Is a Central Demand
In its negotiations with the Big Three Automakers, the United Auto Workers wants to eliminate the lower-tier status hurting many electric vehicle workers. A rank-and-file autoworker explains why the fight is central to a just green transition.
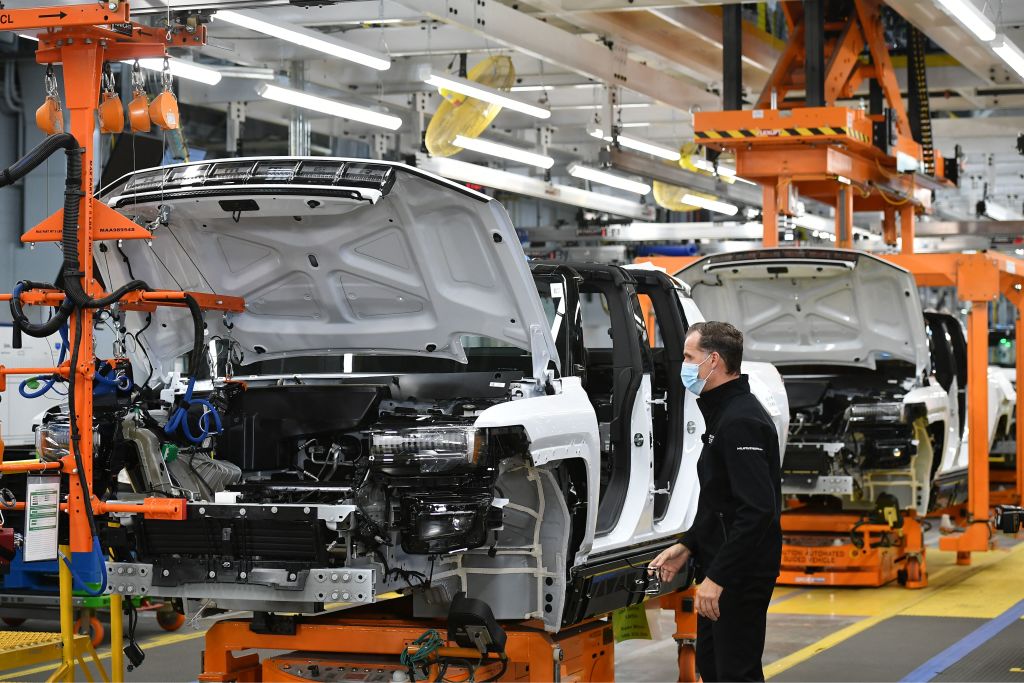
GMC Hummer EVs are seen on an assembly line ahead of a tour by the US president of the General Motors Factory Zero electric vehicle assembly plant in Detroit, Michigan on November 17, 2021. (Mandel Ngan / AFP via Getty Images)
Negotiations between my union, the United Auto Workers (UAW), and the Big Three automakers (Ford, General Motors, and Stellantis) are now underway. UAW president Shawn Fain has already made headlines by demanding a 40 percent raise (much like our CEOs have received), proposing reductions to workweeks that have ballooned to eighty-four hours for some, and tossing Stellantis’s insulting counteroffer into the trash on a livestream video.
Eliminating tiers is the highest priority for many workers. What this means in practice is a bit complicated, especially on the electric vehicle (EV) front. Some EV construction now happens under joint-venture projects like Ultium (General Motors and LG), but tiers under preexisting UAW contracts are already fulfilling much of our EV work. With potentially dozens of battery plants being planned and built in the United States alone, however, that may be changing.
One thing is clear: the elimination of joint-venture battery tiers as well as all other tiers is necessary for a just transition to green manufacturing and infrastructure. Fighting climate change must not come at the expense of workers’ livelihoods — we all deserve the same rights, benefits, and pay won at the bargaining table.
A Labyrinth of Tiers
Tiers are endemic to EV construction across the Big Three. These tiers mean that many workers involved in EV manufacturing suffer from worse pay and benefits and less job security than their counterparts making conventional automobiles.
Of the Big Three, General Motors seems to have the most dizzying array of legal entities covered under our collective bargaining agreements. I’ve heard that EV drive units and batteries are currently made by workers employed by Ford and not some other entity, but I’m willing to bet that Ford’s joint EV venture with SK Innovations, BlueOval SK, would prefer its own contract with UAW similar to Ultium’s. Ditto for StarPlus Energy, Stellantis’s joint venture with Samsung SDI.
General Motors Component Holdings (GMCH) is one such entity where workers are making products for EVs. GMCH Rochester Operations in Rochester, New York, currently builds EV battery cooling lines. GMCH Lockport Operations in Lockport, New York, builds stators for EVs. The remaining GMCH locations do not build components specifically for EVs, but some of what they make are components in all vehicles, and more could be made at all of these plants in the future.
GMCH workers’ starting rate as of the 2019 contract was $16.25 and would max out at $22.50 after a minimum of eight years. I say a “minimum of eight years,” because for purposes of these wage increases, each year actually requires fifty-two “weeks worked.” Many workers experience at least a few months of time being laid off in the span of eight years, which would not count toward this time worked.
Eight years is a long time, especially when you consider that our contracts have a duration of only four years. In the 2015 contract, pay at date of hire remained at $16.25, and only surpassed the old maximum rate of $19.86 after four years of seniority. After a forty-day strike of General Motors in 2019, workers at GMCH locations gained only $2.64 after eight years of seniority had been reached — reaching just under 70 percent of maximum pay for assembly workers. When the 2019 collective bargaining agreement was ratified, it was no surprise that workers at GMCH overwhelmingly rejected it.
The eight-year wage progression is not an outlier among tiers within the UAW–Big Three contracts. Another entity under the master agreement, General Motors Customer Care and Aftersales (GM CCA), has an eight-year progression for workers starting at $17.00 an hour and ending at $31.57 an hour. That is, unless you were hired on or after November 16, 2015: those CCA workers start at $17.00 and top out at just $25.00. CCAs like this one are parts distribution centers that deliver parts for all types of vehicles to dealerships and other repair shops all over North America, and they will be just as important to EVs as they have been for internal combustion engine vehicles.
That brings us to GM Subsystems, a wholly owned subsidiary of General Motors formed in 2009 as part of the restructuring after the federal bailout. My first experience with GM Subsystems was in 2014. Dozens of General Motors temporary workers, many with over two years on the job, received a pay cut and were then classified as GM Subsystems workers. Material movement work, including my own job of sequencing side rearview mirrors, was brought under Subsystems when the local reached a deal with the company upon millions being invested in three new large warehouses to be constructed at Detroit-Hamtramck Assembly where I worked. This is when I learned that concessions don’t even have to wait for when times are lean to rear their ugly head.
In 2016 my plant had absorbed hundreds of workers in preparation for adding a second shift. Most came from Orion Assembly, which had entered retooling for the release of the Chevrolet Bolt. A majority of workers would rather stay at their home plant and would eventually return when they had work for them, but it’s fortunate when a plant within thirty-three miles is able to pick up some nearby laid-off workers. Sometimes that plant is hundreds of miles away, and there is no choice but to move for work, wait it out, or separate from the company entirely.
One of the workers who joined my team then, I learned, was from Brownstown Battery Assembly and had moved over for better pay. While Brownstown was critical to the Volt, the Bolt, and Bolt EUV, the workers there were considered GM Subsystems employees and started at a much lower pay rate, beginning at $15 and ending at $17 after four years.
The Big Three provide workers a profit-sharing benefit, in which autoworkers receive a contribution based on an agreed-upon formula; ours is based on the total North American profits from the previous year. The roughly fifty thousand General Motors workers receive $1 for every million dollars the company makes, rounded down to the nearest $250 — unless they work for GM Subsystems, in which case they only receive $0.25 per million.
Further, profit sharing is based on hours worked. To get the full amount, one must work 1,850 hours over the course of the year, a normal amount unless that worker has been laid off. Depending on the company, workers may not receive more should they work more than 1,850 hours that year. And if you’re a temp, I’m sorry that you’re even hearing about profit sharing, because you’re not getting a dime.
I can say one nice thing about Subsystems’ recent contract: it expires at the same time as the contract for other General Motors workers. So workers across General Motors and Subsystems will be able to stand in solidarity during contract negotiations and possibly a strike, unlike in 2019.
The different tiers of retirement benefits are also labyrinthine. General Motors workers hired after October 15, 2007, do not enjoy a pension or health care in retirement like previous generations did, and they’re instead forced to rely on various schemes of 401(k) and HSA matches and contributions. Even the benefits are uneven between different tiers, with lower-tier workers receiving less generous 401(k) and HSA contributions from the employer.
The Destructive Effect of Tiers
The byzantine tier system also makes it more difficult for autoworkers to find convenient jobs, and it creates inequalities in workplace rights that undermine union solidarity.
Before the Detroit-Hamtramck factory would close in 2020 to be reborn as Factory Zero, there were only a few nearby options for me to transfer to. I was able to put in paperwork to transfer to Flint but not to the much-closer Orion Assembly plant, due to a weird rule there that capped the percentage of tier-one workers. I was offered a job at Lansing, roughly eight-five miles away, but I ended up turning it down due to the distance.
The offer was rescinded anyway due to COVID-19, which provided a job only six miles away from home at Warren Transmission. That plant was shut down in 2019 but was reopened by General Motors for COVID supply manufacturing. I was making masks during the early months of the pandemic, but I was let go in early October for having turned down a job 180 miles away at Fort Wayne Assembly. I apparently was no longer in the correct tier to continue to make masks a short distance from where I live.
I returned home to Detroit-Hamtramck Assembly in July 2021, but many things had changed. For example, just about every material job was now under GM Subsystems, which disappointed General Motors workers who had previously worked those jobs and were now ineligible due to deals we had made during contract negotiations in 2019 to keep work in my plant. All battery assembly fell under GM Subsystems as well, so even if someone wanted to, they could not transfer to jobs in that department.
I want to be clear: I don’t fault anyone for taking Subsystems jobs. That was what our union agreed to, and we’re living with the consequences of accepting lower-tier jobs with severely diminished wages and rights. Those workers not only deserve a living wage but also the respect that comes from having rights on the job.
Those rights are more easily upheld when union members who know their rights fight for those who don’t. I got a crash course in this lesson when I was first hired as a temp in 2006. After hundreds of workers retired following buyouts, CCA Pontiac brought in temps. When temps would get picked on by management, rank-and-file workers with the benefit of seniority kept an eye out and would raise hell — showing what having rights in the workplace looked like.
Unfortunately, workers in battery assembly have lower seniority, and because they’re in a separate part of the building they don’t have nearly enough rank-and-file members looking out for them. Because assembly workers cannot transfer over, there’s a very real “out-of-sight, out-of-mind” effect. On top of that, they have very little in the way of representation. Until recently they’ve had to make do with one steward for their whole unit — a steward who only had thirty hours a week to educate and defend their bargaining unit, the remainder of the time working a job. By comparison, the General Motors workers in the rest of the assembly plant have had a minimum of two full-time stewards since the first large batch of workers returned in July 2021.
In July 2022, contract negotiations ran up until the eleventh hour. The final morning, we were told by our steward that we would have to cross the picket line to leave and return or risk losing our jobs. This was the case for Subsystems workers during the 2019 strike, which caused some tension on the picket lines. It’s a clear example of how tiers erode solidarity and fracture workers’ unity.
With the 2022 contract, pay was raised to a maximum of $22 for materials workers and $24 for battery assemblers, although temporary workers still max at $17 after four or more years. That’s right: we have in writing that workers can be considered temporary for well over four years.
Tiers Must Go
Since the day I was formally hired by GM in 2007, tiers have only gotten more complex and further embedded into our contracts. There was a time when getting your foot in the door in an auto plant meant that you could breathe a sigh of relief. Yes, it takes a while to get used to standing on your feet for most of the day, but barring (sadly common) workplace injuries, your body does eventually get used to the work. But now we have unprecedented amounts of turnover. People hang on in the hope that things might one day get better.
Hopefully, that day is now, with a UAW leadership committed to getting rid of tiers. Eliminating tiers would reduce the number of hours workers have to spend on the job. It would also reduce the years required for workers to retire, and the unnecessary hours workers spend every day driving past workplaces where they would otherwise be able to work.
EVs are an important part of the fight against climate change, and the government is now giving automakers massive amounts of money to build new EV plants. We can’t allow tiers to stay and proliferate in this sector; they are a barrier to a just transition. We should file them in the trash right alongside Stellantis’s initial contract proposal.